In the realm of welding operations, safety stands as an unwavering priority. Welding, a crucial industrial process, demands not only skill and precision but also utmost precaution to protect the well-being of the operators involved. Understanding the hazards inherent in welding and the significance of employing appropriate safety measures can make all the difference in a welding environment.
I. Ensuring Safe Welding Practices and Techniques
A. Equipment Inspection and Maintenance
- Regular inspection of welding machines and accessories is crucial to identify potential hazards and ensure optimal performance.
- Proper maintenance procedures must be followed to uphold safety standards and prevent unexpected breakdowns that could compromise the welding process.
B. Safe Work Area Setup
- Ensuring a clean and clutter-free workspace is a fundamental step in welding safety. A well-organized work area minimizes the risk of accidents and injuries.
- Implementing fire-resistant materials in the surrounding areas provides an additional layer of protection against potential fire hazards.
C. Electrical Safety Measures
- Proper grounding and secure electrical connections are paramount to prevent electrical accidents and shocks during welding operations.
- Protection against electrical hazards involves adherence to safety protocols and the use of appropriate electrical equipment.
D. Welder Training and Competence
- The significance of well-trained welding operators cannot be overstated. Proper training equips welders with essential skills and knowledge to carry out their tasks safely and efficiently.
- Certification and qualification requirements play a vital role in ensuring that welding operators meet industry standards and possess the necessary expertise
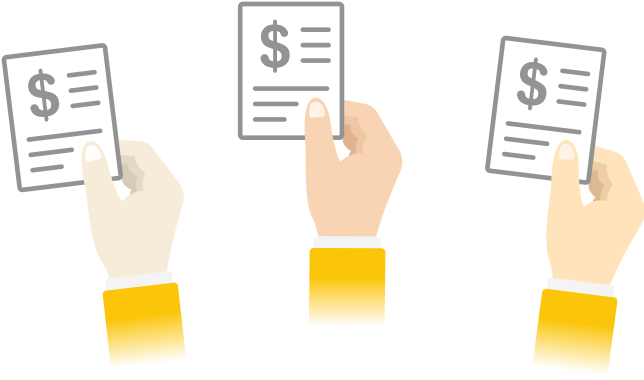
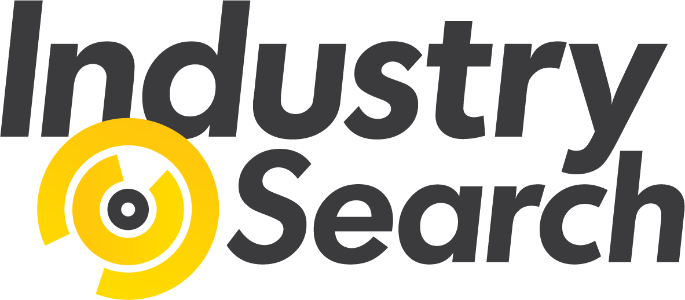
Find the right Welding Machine
Compare quotes from expert Australian suppliers and make the best choice. It's free, quick and easy!
II. Personal Protective Equipment (PPE) for Welding Operators
A. Welding Helmets and Eye Protection
- Importance of Auto-Darkening Helmets
The eyes are particularly susceptible to damage during welding due to the intense light and radiation emitted during the process. Auto-darkening helmets play a critical role in safeguarding welders' vision. These helmets are equipped with sensors that detect the welding arc's light and instantly adjust the lens shade to a darker tint, shielding the operator's eyes from the harmful effects of the arc's brightness.
The benefits of auto-darkening helmets are numerous. They provide a clear view of the workpiece and surrounding area when not welding, eliminating the need to lift the helmet repeatedly. This continuous visual contact enhances efficiency and reduces the risk of accidents. Furthermore, the ability to maintain a constant position without needing to raise or lower the helmet ensures greater accuracy in welding, resulting in higher quality welds.
- Eye Protection against Harmful Radiation
Welders face the potential danger of exposure to harmful ultraviolet (UV) and infrared (IR) radiation emitted during the welding process. Prolonged exposure to these rays can cause serious eye injuries, such as welder's flash (arc eye) or cataracts.
To prevent such injuries, welding helmets must meet safety standards and have a suitable lens shade. The appropriate shade level depends on the welding process and the intensity of the light produced. For instance, shielded metal arc welding (SMAW or "stick welding") emits more intense light than gas metal arc welding (GMAW or "MIG welding"). Therefore, welders must select helmets with the appropriate shade range to ensure adequate protection.
B. Protective Clothing and Gear
- Flame-Resistant Clothing and Gloves
Flame-resistant (FR) clothing is a vital aspect of personal protective equipment for welding operators. Welding processes generate sparks, molten metal, and radiant heat, making non-FR clothing susceptible to catching fire or melting. FR clothing, on the other hand, is designed to resist ignition, self-extinguish, and provide a barrier against heat, preventing burns and injuries.
Welding gloves are another essential component of PPE. They are typically made from leather with added heat-resistant properties, offering protection against sparks, heat, and sharp objects. Welding gloves should fit well and allow dexterity, enabling welders to handle materials and welding equipment with ease and safety.
- Proper Attire for Welding Operations
In addition to FR clothing and gloves, welders should wear long-sleeved shirts and long pants made from non-flammable materials to cover exposed skin. The clothing should fit comfortably but not be overly loose to prevent potential entanglements with equipment or the workpiece.
To further protect against hazards, welders should avoid wearing jewelry, especially on hands and wrists, and tie back long hair. These precautions reduce the risk of snagging or injury during welding tasks.
C. Respiratory Protection
- Respirators for Fume and Particle Filtration
During welding, various fumes, gases, and particles are generated, depending on the materials being welded. These airborne contaminants can pose significant health risks if inhaled regularly or in large quantities. Respirators are crucial in mitigating these risks and protecting the respiratory system of welding operators.
Respirators equipped with filters specifically designed for welding fumes are highly effective in capturing harmful particles and fumes. Depending on the welding process and materials used, different types of respirators may be required. It is essential to choose the appropriate respirator and ensure it fits snugly on the face for maximum protection.
- Avoiding Respiratory Health Risks in Welding
Respiratory health risks associated with welding include metal fume fever, chronic bronchitis, and even more severe conditions such as lung cancer. To minimize exposure to welding fumes, welders should work in well-ventilated areas or utilize local exhaust ventilation systems. Properly maintained ventilation systems can help to reduce the concentration of fumes in the air, providing a healthier work environment for welding operations.
III. Proper Ventilation and Fume Extraction in Welding Environments
A. Importance of Adequate Ventilation
Welding processes generate hazardous fumes and gases that can pose serious health risks to welding operators and those in the vicinity. Adequate ventilation is paramount to maintaining a safe working environment and minimizing exposure to welding fumes. In this section, we will explore the significance of proper ventilation and its role in ensuring the well-being of welding personnel.
- Reducing Exposure to Welding Fumes
Welding fumes are a complex mixture of particles and gases that are produced when metals are heated and melted during the welding process. These fumes often contain harmful substances, such as metal oxides, fluorides, and other toxic compounds, depending on the materials being welded. Prolonged exposure to welding fumes can lead to various health issues, including respiratory problems, lung damage, and even long-term illnesses.
By implementing effective ventilation systems, welding operators can significantly reduce their exposure to these hazardous fumes. Adequate ventilation helps disperse and remove the fumes from the work area, preventing them from accumulating and reaching harmful levels. This is particularly crucial in confined spaces or areas with poor air circulation.
- Methods for Effective Ventilation
There are several methods to achieve effective ventilation in welding environments, each tailored to the specific welding setup and workspace. Two common approaches are:
- Local Exhaust Ventilation (LEV): Local exhaust ventilation, often referred to as fume extraction, involves using specially designed hoods and ducts to capture welding fumes at the source. These ventilation systems are positioned close to the welding arc to capture the fumes before they disperse into the surrounding air. The collected fumes are then directed through filters to remove harmful particulates and gases, ensuring that only clean air is released back into the workspace.
- General Dilution Ventilation: General ventilation, also known as dilution ventilation, involves the use of fans or natural airflow to dilute and disperse welding fumes throughout the workspace. This method is particularly useful in larger welding areas where local exhaust systems may not be practical. By continuously introducing fresh air and exhausting contaminated air, general ventilation helps maintain a safer overall working environment.
In either approach, the selection and design of the ventilation system should consider the welding process, the materials being welded, the welding location, and the number of welding operators. Regular maintenance and inspection of these systems are crucial to ensure their optimal performance and effectiveness in safeguarding the health of everyone involved.
B. Fume Extraction Systems
Fume extraction systems play a pivotal role in removing welding fumes and protecting workers from inhaling harmful airborne contaminants. These systems come in various types, each offering specific benefits depending on the welding application and operational needs. Additionally, proper positioning and maintenance of these systems are essential to maximize their efficiency and maintain a safe work environment. In this section, we will explore the different types of fume extractors and the considerations for their positioning and maintenance.
Types of Fume Extractors and Their Benefits
- Portable Fume Extractors: Portable fume extractors are flexible and versatile units that can be easily moved around the workspace as needed. These extractors are particularly useful for welding tasks that require mobility or when there are multiple welding stations. They offer localized fume extraction capabilities, capturing welding fumes right at the source, and can accommodate various attachment accessories for specific applications.
- Fixed Fume Extractors: Fixed fume extraction systems are permanently installed in the welding facility and provide continuous ventilation for specific workstations or welding bays. These systems offer stable and consistent fume extraction, ensuring that the welding operators are protected throughout their work. They are ideal for high-volume welding operations and where welding processes are regularly performed in the same location.
- Downdraft Tables: Downdraft tables are specialized workstations equipped with integrated fume extraction systems. The surface of these tables features perforations that allow welding fumes to be drawn downward effectively. Downdraft tables are particularly beneficial for smaller welding tasks, as they offer localized fume control and prevent fumes from spreading into the surrounding environment.
- Centralized Fume Extraction Systems: Centralized fume extraction systems are designed to serve multiple workstations or an entire welding facility from a centralized unit. They are highly efficient for large-scale welding operations and ensure comprehensive fume removal across the facility. These systems can be customized to meet specific operational requirements, making them a cost-effective choice for significant welding setups.
Positioning and Maintenance of Fume Extraction Units
The positioning of fume extraction units is crucial to their effectiveness. For local exhaust systems, the hood or capture device should be positioned as close to the welding arc as possible to efficiently collect the fumes. Proper positioning ensures that a maximum amount of harmful fumes is captured before they disperse into the workspace.
Regular maintenance of fume extraction systems is essential to keep them in optimal working condition and guarantee effective fume removal. Maintenance tasks include replacing filters, cleaning ducts, and inspecting the entire system for wear and tear. Timely maintenance not only prolongs the life of the equipment but also ensures that the system consistently provides a safe and healthy working environment.
IV. Hazard Mitigation and Risk Assessment in Welding Operations
A. Identifying Welding Hazards
Welding operations pose inherent risks that demand a comprehensive understanding of potential hazards. Identifying these risks is the first crucial step towards creating a safe welding environment. By recognizing the common hazards associated with welding workplaces, operators and supervisors can proactively implement safety measures to protect personnel and property.
Common Hazards in Welding Workplaces
- Welding Fumes and Gases: The process of welding generates fumes and gases that contain harmful substances such as metal oxides, ozone, and nitrogen oxides. Prolonged exposure to these fumes can lead to respiratory issues and other health concerns.
- Welding Arc and Radiation: The intense heat produced during welding emits powerful electromagnetic radiation, including ultraviolet (UV) and infrared (IR) rays. Direct exposure to the welding arc can cause eye injuries, skin burns, and long-term damage.
- Fire and Explosion Risks: Welding involves the use of high heat, sparks, and flammable materials, making it susceptible to fire hazards. Additionally, the presence of combustible gases or chemicals in the vicinity increases the risk of explosions.
- Electrical Hazards: Welding machines operate on high electrical currents, making the risk of electrical shocks or electrocution a significant concern.
- Noise and Vibration: Welding operations can produce loud noise levels and vibrations, potentially leading to hearing impairment and other health issues for workers.
Risk Assessment and Management
Once potential hazards are identified, a systematic risk assessment must be conducted to evaluate the severity of each risk and determine appropriate control measures. A risk assessment typically involves the following steps:
- Hazard Identification: Thoroughly inspect the welding workplace and processes to identify potential hazards, as mentioned above.
- Risk Analysis: Assess the likelihood and potential consequences of each identified hazard. This analysis helps prioritize risks based on their severity.
- Control Measures: Implement control measures to minimize or eliminate risks. These measures can include engineering controls (e.g., fume extraction systems), administrative controls (e.g., safe work procedures), and personal protective equipment (PPE) usage.
- Training and Education: Ensure that all personnel involved in welding operations are adequately trained to recognize hazards and follow established safety protocols.
- Monitoring and Review: Regularly monitor the effectiveness of implemented control measures and review risk assessments to adapt to changing circumstances or identify emerging hazards.
B. Implementing Safety Measures
After identifying potential hazards and assessing risks, the next imperative is to establish robust safety measures that will protect welding personnel and assets. These measures encompass a combination of engineering controls, administrative procedures, and emergency response planning.
Control Measures to Minimize Risks
- Ventilation and Fume Extraction: Installing effective ventilation systems and fume extractors ensures the removal of hazardous welding fumes and gases from the work area, reducing the risk of respiratory issues.
- Welding Screens and Curtains: Using welding screens and curtains can contain sparks and splatter, protecting nearby workers and preventing potential fire hazards.
- Personal Protective Equipment (PPE): Equipping welding operators with appropriate PPE, such as welding helmets with auto-darkening filters, flame-resistant clothing, gloves, and respirators, provides essential protection against welding-related hazards.
- Machine Maintenance and Inspections: Regular maintenance of welding machines and equipment helps prevent malfunctions and reduces the risk of accidents caused by faulty machinery.
Emergency Response Planning
Despite the most stringent safety measures, unforeseen incidents can still occur. Therefore, it is critical to have comprehensive emergency response plans in place:
- Training and Preparedness: Conduct regular training sessions to educate welding operators and other personnel on emergency response procedures, including proper evacuation protocols.
- Fire Safety Equipment: Ensure the availability and accessibility of fire extinguishers, fire blankets, and other firefighting tools in welding areas.
- First Aid Stations: Establish designated first aid stations with necessary medical supplies in case of injuries.
- Emergency Contact Information: Display emergency contact numbers, including those for medical assistance and fire departments, in prominent locations.
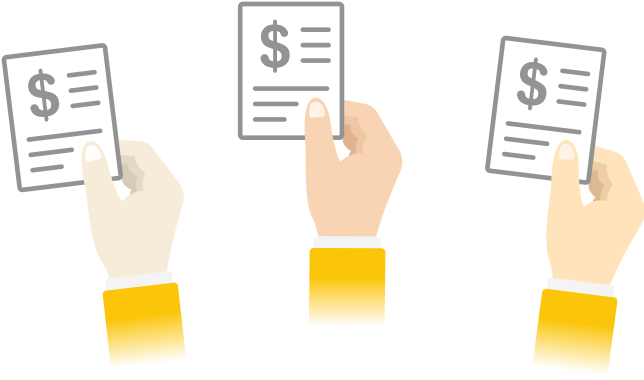
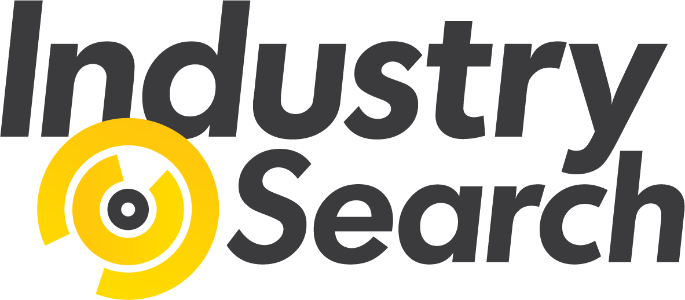
Find the right Welding Machine
Compare quotes from expert Australian suppliers and make the best choice. It's free, quick and easy!
V. Fire Safety and Emergency Protocols in Welding Areas
A. Fire Prevention and Precautions
Fire safety is of utmost importance in welding areas, where the combination of intense heat and flammable materials can create potential fire hazards. By following proper preventive measures and taking necessary precautions, welding operators can significantly reduce the risk of fires during welding operations. This section outlines essential fire prevention steps and safety measures to ensure a secure working environment.
- Preventing Fires During Welding: To prevent fires during welding, operators must be proactive and attentive throughout the welding process. Here are some key steps to minimize the risk of fire incidents:
- Clear the Area: Before initiating any welding activity, ensure that the workspace is free from flammable materials, debris, and other combustible substances. Store flammable materials in designated, fire-resistant containers away from the welding area.
- Fire-Resistant Barriers: Create fire-resistant barriers using welding blankets or curtains to shield nearby flammable objects from sparks and heat generated during welding.
- Use Correct Welding Techniques: Employ proper welding techniques to reduce the amount of spatter and sparks produced during the process. This can be achieved by maintaining the appropriate distance between the electrode and the workpiece.
- Monitor Surroundings: Continuously monitor the surrounding environment during welding. If any sign of fire or smoldering is observed, immediately stop the welding process and address the issue before continuing.
- Fire Watches: For particularly high-risk welding operations, consider implementing a "fire watch" system. A designated individual should be responsible for observing the work area for a period after welding to ensure no fires have started.
- Fire Extinguisher Placement and Training
It is equally important to provide comprehensive training to all welding operators and personnel on the proper usage of fire extinguishers. Training should cover:
- Understanding Fire Classes: Educate operators about the various classes of fires and the specific extinguisher appropriate for each type.
- Proper Handling: Train personnel on the correct way to handle a fire extinguisher, including how to aim, squeeze, sweep, and control the extinguishing agent's discharge.
- Emergency Response: Instruct individuals on the actions to take in case of a fire emergency, including raising an alarm, contacting emergency services, and implementing evacuation procedures.
By adhering to these fire prevention and precautionary measures, welding operators can create a safer work environment and reduce the likelihood of fire incidents during welding operations.
B. Emergency Procedures
Despite taking all necessary precautions, emergencies can still occur in welding areas. Therefore, it is imperative to establish clear and effective emergency procedures to promptly respond to any unforeseen incidents. Properly trained personnel and a well-defined emergency action plan can make a significant difference in mitigating potential risks and ensuring the safety of everyone present.
Evacuation Plans and Assembly Points
Welding facilities should have well-documented evacuation plans that detail escape routes and assembly points. The evacuation plan should be prominently displayed, and all employees and visitors must be familiar with its contents.
- Escape Routes: Identify primary and secondary escape routes from the welding area to safe outdoor locations. The escape routes should be free from potential obstructions and clearly marked with illuminated signs.
- Assembly Points: Designate assembly points at a safe distance from the welding area. These points provide a secure location for personnel to gather during evacuations, allowing for headcounts and ensuring that everyone is accounted for.
- Emergency Drills: Conduct regular emergency evacuation drills to familiarize employees with the evacuation process and reinforce their understanding of the escape routes and assembly points.
- Dealing with Welding-Related Accidents and Emergencies
In the event of a welding-related accident or emergency, swift and decisive action is essential. Proper training and adherence to predetermined protocols can help minimize the impact of the situation. Here are the steps to follow in case of an emergency:
- Assess the Situation: Remain calm and assess the severity of the emergency. Determine the appropriate response based on the type of incident, such as fire, injury, or equipment malfunction.
- Activate Alarm and Alert Others: If the emergency is beyond your immediate control, activate the alarm system to alert others in the vicinity. Inform nearby coworkers and, if necessary, communicate with a central control point or supervisor.
- Provide First Aid: If there are injuries, administer immediate first aid, if you are trained to do so, while waiting for medical professionals to arrive.
- Report the Incident: Notify the appropriate authorities and supervisors about the incident, providing specific details about what has occurred.
- Follow Emergency Procedures: Adhere to the established emergency procedures and await further instructions from designated personnel or emergency services.
VI. Training and Certification for Welding Machine Operators
A. The Value of Proper Training
Welding is a highly specialized skill that requires comprehensive training to ensure safe and efficient operations. Proper training for welding machine operators holds paramount importance in the welding industry. This section explores the numerous benefits that come with formal welding training programs and emphasizes the significance of continual learning and skill development.
Benefits of Formal Welding Training Programs
Formal training programs provide aspiring welders with a structured and systematic approach to learning the craft. These programs are designed to impart the necessary theoretical knowledge and hands-on practical experience essential for becoming proficient in welding techniques. The benefits of such programs include:
- Comprehensive Instruction: Formal training covers a wide range of welding processes, safety protocols, and best practices. This knowledge equips welding operators to handle various welding tasks and challenges competently.
- Skill Enhancement: Through hands-on training, individuals have the opportunity to refine their welding skills under the guidance of experienced instructors. This practice not only improves the quality of welds but also enhances the operator's confidence in their abilities.
- Safety Emphasis: Proper training emphasizes welding safety and the correct use of personal protective equipment (PPE). Operators are trained to identify potential hazards and adopt safe practices to prevent accidents and injuries.
- Industry Relevance: Reputable training programs are designed in alignment with industry standards and advancements. Graduates of such programs are better prepared to meet the demands of the welding profession and contribute effectively to their employers' success.
- Employment Opportunities: Welding operators who have completed formal training are often more attractive to employers. Certification from recognized training institutes can act as a stepping stone for career advancement and job opportunities.
Continual Learning and Skill Development
The field of welding is dynamic and continuously evolving with advancements in technology and industry requirements. As such, welding machine operators must embrace a culture of continual learning to stay current with the latest developments in the field. Continual learning allows welding professionals to:
- Adapt to Technological Advancements: New welding techniques, equipment, and materials are regularly introduced. Ongoing learning enables operators to adapt to these changes, making their work more efficient and effective.
- Enhance Problem-Solving Abilities: Welding often involves complex challenges that require critical thinking and problem-solving skills. Continued education hones these abilities, allowing operators to overcome obstacles with confidence.
- Stay Updated on Safety Standards: Safety regulations may evolve over time, and staying informed is crucial to maintaining a secure work environment. Regular training ensures that welding operators are up-to-date with safety protocols and practices.
- Pursue Specializations: Advanced training programs offer opportunities for specialization in specific welding processes or industries. This expertise can open doors to specialized job roles and potentially higher earnings.
B. Certification and Compliance
In addition to training, welding machine operators must obtain certifications to validate their skills and competence. This section explores industry-recognized certifications for welders and highlights the importance of meeting safety standards and legal requirements.
-
Industry-Recognized Certifications for Welders
Certifications play a crucial role in verifying the expertise and proficiency of welding operators. They serve as tangible evidence of a welder's capabilities and are highly regarded by employers and clients alike. Some of the most common certifications include:
- Certified Welder (CW): This certification is awarded by the American Welding Society (AWS) and attests to a welder's ability to perform specific welding procedures.
- Certified Welding Inspector (CWI): Also awarded by AWS, the CWI certification is for individuals who inspect and assess welding work to ensure compliance with quality standards and codes.
- Certified Welding Educator (CWE): The CWE certification is designed for welding instructors and educators, validating their expertise in teaching welding techniques and safety.
- Manufacturer-Based Certifications: Some welding equipment manufacturers offer certifications specific to their machines or processes. These certifications demonstrate a welder's proficiency in handling their equipment.
-
Meeting Safety Standards and Legal Requirements
Certifications often come with a requirement to adhere to safety standards and industry regulations. Compliance with these standards is not only essential for maintaining certification but also for ensuring the safety of welding operations. Welding machine operators must be aware of and follow guidelines related to:
- Personal Protective Equipment (PPE): Proper selection and use of PPE, such as welding helmets, gloves, and protective clothing, are critical for safeguarding against potential hazards.
- Ventilation and Fume Extraction: Adequate ventilation and fume extraction systems are necessary to minimize exposure to harmful welding fumes and gases.
- Welding Area Safety: Maintaining a clean, organized, and hazard-free work area contributes to accident prevention and enhances overall productivity.
- Electrical Safety: Welders must be knowledgeable about electrical hazards and take precautions to prevent electrical accidents.
- Fire Safety: Implementing fire prevention measures and being prepared for potential welding-related fires are essential aspects of welding safety.
In conclusion, the realm of welding operations places paramount importance on safety as an unwavering priority. Welding, a critical industrial process, requires not only skill and precision but also utmost precaution to safeguard the well-being of operators involved. Recognizing the potential hazards inherent in welding and the significance of implementing appropriate safety measures can truly make a difference in a welding environment. By ensuring safe welding practices through equipment inspection, proper work area setup, adherence to electrical safety measures, and comprehensive welder training, the risks associated with welding can be significantly minimized. Moreover, the utilization of personal protective equipment (PPE) such as auto-darkening helmets, flame-resistant clothing, and respiratory protection adds an extra layer of defense against the harmful effects of welding processes. Adequate ventilation and fume extraction systems play an essential role in reducing exposure to hazardous fumes and gases, further enhancing the safety of welding environments. Additionally, identifying welding hazards, conducting risk assessments, and implementing control measures contribute to the comprehensive management of risks. Proper training, certification, and compliance with safety standards underscore the commitment to creating a safe and productive welding environment. Through continuous learning, adherence to best practices, and a thorough understanding of emergency protocols, welding machine operators can uphold safety standards, protect themselves and their colleagues, and contribute to a safer and more secure welding industry.