Deciding to have a liquid filling machine upgrade from manual filling often comes with anxiety about the ROI and the high upfront investment.
When done at the right time and under the right circumstances, improving your production line will set you off to a good start in scaling your business. The big question is, when is the best time to get an upgrade?
Signs Your Business Needs an Upgrade
Often, things that trigger the thoughts of improving a production line are increased production demands, compromised product quality, constant labour costs issues, and manual process inefficiency.
Take a closer look at these issues and consider them as a checklist to help you decide on your next move for your business.
#1 Increasing Production Demand
Rising customer demand can outstrip the capabilities of manual or outdated filling machines. When the demand is too high and the supply chain is struggling to keep the customers happy, the risks are damaged customer trust and a tarnished brand reputation.
A big chunk of the operational costs in the manual filling business is labour costs. If you’ve done all the labour optimisation to account for the large volume of orders, maybe it’s your cue to automate some repetitive processes like packaging and filling to machines and using manpower for other critical tasks.
One good example of efficient automation is how The Marshmallow Co. invested in a packing machine to pack all their marshmallows and allocate their manpower to cooking and preparing the food. It helped them maximise the utilisation of their staff and ensure consistency in the packaging of their products.
#2 Frequent Downtime and Maintenance
Frequent machine breakdowns and maintenance from outdated filling machines are a constant headache and a significant drain on resources. Constant repairs not only disrupt production schedules but also run the risk of getting the brand cancelled by disappointed consumers.
While efficiency is the name of the game, it’s wise to consider a new investment if the repair costs and the negative feedback become at par with the costs of replacing the equipment. The thing is, the liquid filling machine upgrade doesn’t have to be new equipment.
Used machinery that is still efficient and has robust parts is a good option. You may look for closing companies who sell their still-working equipment for a cheaper price.
#3 Inconsistent Product Quality
The most expensive asset of a business is the customer’s trust. If you’re receiving valid complaints about inconsistent fills, it may start to damage your brand’s image and bottom line. The causes of these volume differences and inconsistent fills are categorised into two factors:
-
Repairable concerns: Some concerns can still be repaired and addressed with low-cost maintenance and cleaning like clogged pistons and air trapped in the machine. These can be called to the customer service of your old machine provider.
Another key step in maintaining consistent product fills is the implementation of regular preventive maintenance. One study conducted by C K Adarsh and Sudheer D Kulkarni proved that regular preventive maintenance provides enhanced productivity.
-
Permanent damages: The grounds for the replacement of outdated liquid filling machines are the worn-down parts that have seen better days.
Since different types of liquid and viscosities (liquid thickness) run on these parts, they erode over time, causing inefficiencies and inconsistency in filling products.
Whenever there’s an inconsistent fill, it pays to use the Define-Measure-Analyze-Improve-Control (DMAIC) approach to evaluate if the problem can be solved through repairs and maintenance or if you’re already dealing with permanent damages that require equipment replacement.
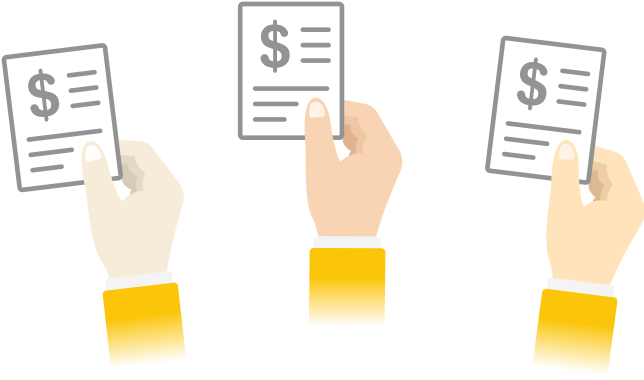
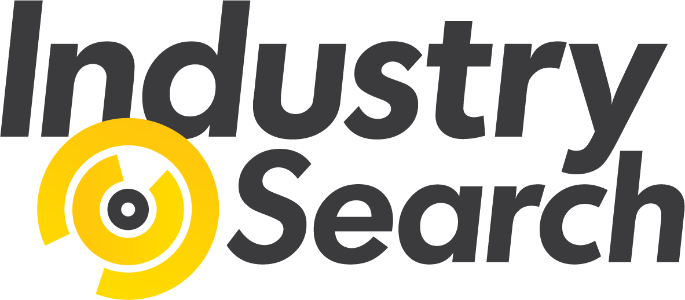
Find the right Liquid Filling Machine
Compare quotes from expert Australian suppliers and make the best choice. It's free, quick and easy!
Benefits of Upgrading to Modern Liquid Filling Machines
Grasp the full implication of investing in a new or used liquid filling machine upgrade by also looking into its benefits in your production line.
#1 Enhanced Efficiency and Productivity
Modern liquid filling machines can significantly increase production speed and reduce labour costs. They are often automatic with user-friendly interfaces for easy calibration.
These machines are equipped with sensors for better precision in filling products and have robotics integration, making production less labour-intensive. They can also be controlled remotely and handle different liquid consistencies.
Most modern liquid filling machines can also handle different levels of viscosities which is crucial if you are planning on offering varying liquid products in the future.
#2 Improved Accuracy and Consistency
Technological advancements in liquid filling machines ensure precise fills using sensors and calculated timeframes for filling accuracy. The end products are usually cleaner and more consistent in volume which builds customer trust and loyalty that are vital for long-term business success.
#3 Scalability and Flexibility - Future-proofing
Modern filling machines can easily adapt to different product types and volumes, providing the flexibility needed for diverse production requirements. This scalability allows businesses to be future-proof and grow without major production overhauls. The equipment’s ability to adapt ensures a smooth transition as demand for your product increases.
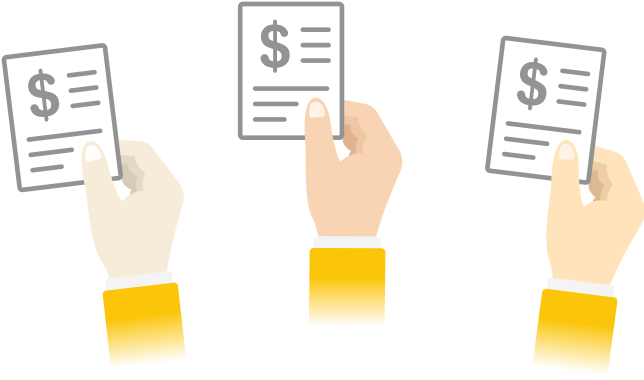
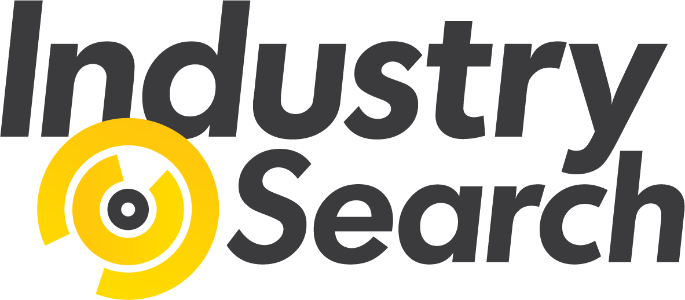
Find the right Liquid Filling Machine
Compare quotes from expert Australian suppliers and make the best choice. It's free, quick and easy!
Factors to Consider Before Upgrading
Equipment costs a hefty amount of money, which means you have to study the upgrade carefully. Here are some of the things you have to look into before venturing into automation.
1. Cost-Benefit Analysis
A detailed cost-benefit analysis can be difficult since it’s not always easy to forecast the ROI. Factors to consider include:
- Demand
- Current operational costs
- Projected increase in production
- Gross income
- Scalability of the machine
A business can accurately estimate the long-term savings and return on investment (ROI) from such an upgrade with a thorough financial analysis. It is weighing the costs of liquid filling machine upgrades versus the gross income of the company.
The sustainable percentage to consider is to invest in equipment that costs less than 50% of your gross income. The most ideal percentage is around 20%. However, you should not stick to that percentage and be flexible in your strategy.
According to Colbey Pfund from Forbes, reinvesting in your business should be diversified. Pfund said, “Each area of your business will need money but you need to maintain a delicate balance. Invest too much in one area and you’ll be left short when another area desperately needs a cash infusion. ”
Conduct a financial analysis on the costs of repair and maintenance of outdated or manual filling processes, including losses when the machines break down or when the production gets understaffed. Other bases are the lifespan of the machine and the sustainability of its parts or features.
2. Compatibility with Existing Systems
Considering the investment is only one part of the process. You have to thoroughly check every step on how to complement the new liquid filling machine process in the following aspects:
- Facility adjustments to accommodate the liquid filling machines
- Process adjustments in the production line
- Training of management and staff
- Calibration and modification of the machine for your products
- Compatibility with the current process (combination of labour and automated work)
- Liquid consistency thresholds
- Policy and regulation compliance
The integration must be carefully planned to ensure proper procurement of new equipment, testing, and integration. The last thing you want is to purchase equipment that won’t perfectly blend or complement your production line.
3. Supplier Reputation and Support
Choosing a reliable supplier with good after-sales support is vital. Research supplier reputation and customer feedback to make an informed decision. You may consider talking to a handful of liquid-filling equipment suppliers from different companies to check your options.
Making the Transition Smooth
After the purchase, your comprehensive production upgrade plan must include the transition from your old process to the semi or fully-automated process. Here are some general factors to consider.
#1 Training and Support for Staff
Proper training ensures employees can use new equipment effectively. Proper calibration, training, and pilot testing are crucial to bridge the knowledge gap in handling new equipment.
Conduct dry runs and staggered shift adjustments to production staff or transition by phases to give them enough time to learn the ropes of automation. Take note that equipment handling poses health hazards and may cause harm or injury if not properly used.
It's important to consider the learning curve of your production staff in handling the new tech. Ensure that you create some turn points where you can assess their level of understanding of the equipment. Proper training ensures that your staff is well-equipped to confidently handle the new tech should it encounter issues.
#2 Phased Implementation
A gradual transition helps avoid major production disruptions for your business. Therefore, plan and execute a phased upgrade to ensure smooth operations and minimal downtime. The production team, marketing, and customer relations must be aligned during the transition to ensure everything is ready in case things don’t go as planned.
#3 Regular Monitoring and Maintenance
Establish a regular maintenance schedule for new machines to maximise their lifespan and efficiency. Usually, the integration can be stressful and may be longer than usual. Therefore, communication with your supplier must be stated as part of the expectations as you monitor performance and address issues promptly for undisrupted productivity.
Speed up the procurement process with IndustrySearch
Finding suppliers is a tough process on its own. Instead of manually looking for a liquid-filling machine supplier in Australia, we’ve verified and partnered with expert suppliers on one seamless platform so that you can easily get multiple quotes.
Find the right liquid filling machine supplier and get a quote today so you can allot your time to more productive tasks in your business.