Investing in an efficient pallet wrapping machine can significantly boost productivity and profitability for businesses that handle a high volume of palletized products.
However, with the array of machine types, capabilities, and pricing options on the market, selecting the right pallet wrapper requires careful evaluation of needs and key factors.
This comprehensive buying guide provides Australian businesses, particularly those in Sydney, with expert advice on choosing the optimal pallet wrapping machine in Sydney.
1. Assessing Packaging Needs and Requirements
When it comes to optimizing your pallet wrapping process, selecting the right pallet wrapping machine is crucial.
Pallet wrapping machines in Australia come in various types and configurations, each catering to specific packaging needs and requirements.
Here is everything you need to know to make an informed decision when it comes to assessing the packaging needs and requirements.
1.1 Understanding Your Packaging Needs
Before diving into the world of pallet wrapping machines, it is vital to have a clear understanding of your packaging needs. Conducting a thorough assessment of your requirements will help you identify the specific features and capabilities your ideal machine should possess. Consider the following points:
Load Size and Weight: Determine the average size and weight of the loads you need to wrap. This information will impact the machine's capacity and overall performance.
Packaging Volume: Analyze the volume of pallets you wrap daily, weekly, or monthly. High-volume operations may benefit from fully-automatic machines, while semi-automatic machines could be suitable for smaller businesses.
Product Characteristics: Take into account the nature of the products you are wrapping. Some items may require special handling or precautions during the wrapping process.
Packaging Environment: Consider the environment in which the pallet wrapping machine will operate. Factors like humidity, dust, and temperature can influence the machine's durability and maintenance requirements.
1.2 Pallet Wrapping Machine Features
Now that you have a comprehensive understanding of your packaging needs, it's time to explore the various features offered by pallet wrapping machines. Each feature serves a specific purpose, so prioritizing them based on your requirements is essential. Key features to look out for include:
Turntable Size and Speed: The turntable is the rotating platform on which the pallet sits during the wrapping process. Assess the turntable's size and speed to ensure it accommodates your pallet dimensions and meets your desired wrapping speed.
Film Carriage System: The film carriage system holds and dispenses the stretch film during wrapping. Different machines may offer varying film carriage options, such as powered pre-stretch or mechanical pre-stretch, which we'll explore in more detail later.
Control Panel and Automation: Consider the ease of use and automation capabilities of the machine's control panel. User-friendly interfaces can reduce training time and improve overall efficiency.
Safety Features: Safety should be a top priority in any packaging operation. Look for features like emergency stop buttons, safety barriers, and sensors to enhance workplace safety.
1.3 Compatibility with Wrapping Materials
While assessing your packaging needs, it's crucial to consider the compatibility of your chosen pallet wrapping machine with different wrapping materials. Pallet wrapping machines typically use stretch films, but some machines can also handle other wrapping materials such as netting or shrink wrap. Here are some points to keep in mind:
Stretch Film: Stretch film is the most common and versatile wrapping material. It provides excellent load stability, and its elasticity allows for tight and secure wraps. Ensure the machine you choose can handle the desired width and thickness of stretch film.
Netting: Some applications may require the use of netting for ventilation or airflow. Check if the machine can accommodate netting rolls of various sizes.
Shrink Wrap: While less common for pallet wrapping, shrink wrap may be necessary for specific product types. If you foresee using shrink wrap, verify if the machine supports this material.
1.4 Budget and Space Constraints
As with any business investment, budget and space constraints play a significant role in your decision-making process. Pallet wrapping machines come in various price ranges, depending on their features and capabilities. Consider the following aspects to align your selection with your budget:
- Machine Type: Fully-automatic pallet wrapping machines generally come with a higher price tag than semi-automatic ones. Assess your budget and evaluate which type suits your financial capacity.
- Long-term ROI: Remember that while fully-automatic machines may have a higher upfront cost, they can offer significant long-term ROI through increased efficiency and reduced labor costs.
- Available Space: Measure the available space in your facility to ensure the chosen machine fits comfortably and does not disrupt other operations.
Assessing your packaging needs and requirements is the crucial first step in finding the perfect pallet wrapping machine for your business.
By understanding your load characteristics, volume, and budget, you can narrow down the options and focus on the features that truly matter.
Keep in mind the compatibility with different wrapping materials, and don't forget to prioritize safety features to create a secure and efficient packaging process.
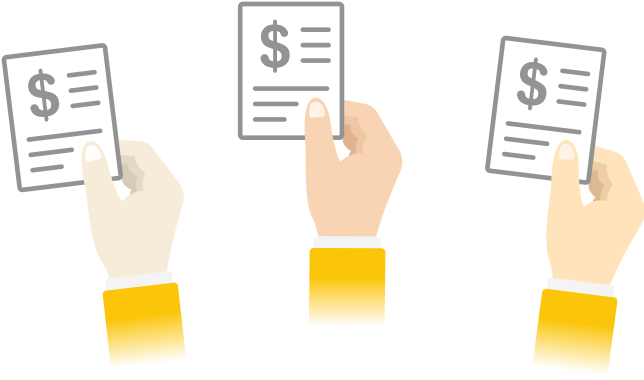
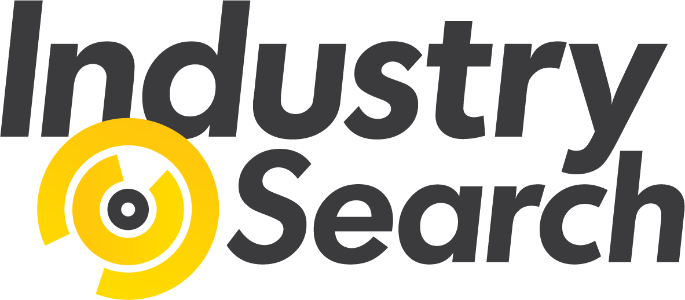
Find the right Pallet Wrapping Machine
Compare quotes from expert Australian suppliers and make the best choice. It's free, quick and easy!
2. Considering Pallet Wrapping Machine Types: Semi-automatic vs. Fully-automatic
Once you have thoroughly assessed your packaging needs and requirements, the next crucial step is to choose the right type of pallet wrapping machine.
In Australia, you will come across two main types: semi-automatic and fully-automatic machines.
Each type offers distinct advantages and functionalities, so understanding their differences and benefits is essential to make an informed decision for your business.
Lets look at features and characteristics of both types to help you determine which one aligns best with your operational needs.
2.1 Semi-Automatic Pallet Wrapping Machines
Semi-automatic pallet wrapping machines are a popular choice for businesses with moderate packaging volumes and those seeking a balance between manual labor and automation. These machines require some level of human intervention during the wrapping process.
Let's explore the key characteristics of semi-automatic pallet wrapping machines:
- Load Placement and Start: In a semi-automatic machine, an operator places the pallet load on the turntable and starts the wrapping process. While this requires manual effort, it provides the operator with control over load positioning and film application.
- Film Application: The operator attaches the film to the load and activates the wrapping cycle, which then applies the film around the pallet automatically. Some machines offer features like automatic film cutting and film clamp to simplify the process.
- Flexibility and Control: Semi-automatic machines offer flexibility, as they can wrap pallets of various sizes and shapes. Operators can adjust wrapping parameters and add extra layers of film if needed, depending on the load requirements.
- Cost-Effectiveness: Compared to fully-automatic machines, semi-automatic models generally have a lower initial cost, making them more accessible to businesses with budget constraints.
2.2 Fully-Automatic Pallet Wrapping Machines
Fully-automatic pallet wrapping machines take automation to the next level, providing a hands-free and seamless packaging experience. These machines are ideal for high-volume operations that require consistent and efficient wrapping. Below are the primary features of fully-automatic pallet wrapping machines:
- Automated Load Handling: With fully-automatic machines, a conveyor system or forklift automatically places the pallet on the turntable, and the machine takes care of the entire wrapping process, from start to finish.
- Advanced Control Systems: These machines come equipped with sophisticated control systems that allow for customization of wrapping patterns, film tension, and other settings. This level of control ensures precise wrapping tailored to specific load requirements.
- High Throughput: Fully-automatic machines boast high wrapping speeds, significantly increasing the number of pallets that can be wrapped per hour compared to semi-automatic models.
- Reduced Labor Requirements: Since these machines handle most aspects of the wrapping process autonomously, they can help reduce labor costs and free up employees for other tasks.
- Consistency and Uniformity: The automated nature of fully-automatic machines ensures consistent and uniform wrapping, reducing the risk of load shifting during transportation.
2.3 Choosing Between Semi-Automatic and Fully-Automatic Machines
Selecting the right type of pallet wrapping machine depends on several factors specific to your business. Consider the following points to guide your decision-making process:
- Packaging Volume: If your business wraps a relatively low number of pallets per day or has fluctuating packaging volumes, a semi-automatic machine may be sufficient.
- Labor Costs: Assess your labor costs and availability. Fully-automatic machines can help offset higher upfront costs through labor savings in the long run.
- Load Variability: If you frequently handle diverse load sizes and shapes, a semi-automatic machine's flexibility and manual control may be advantageous.
- Throughput Demands: For high-volume operations that require rapid and consistent wrapping, a fully-automatic machine can significantly improve productivity.
- Long-Term Growth: Consider your business's growth projections. Investing in a fully-automatic machine may be a strategic decision for future scalability.
When it comes to pallet wrapping machines, the choice between semi-automatic and fully-automatic largely depends on your packaging volume, labor costs, load variability, and long-term growth plans. Semi-automatic machines offer flexibility and cost-effectiveness, making them suitable for businesses with moderate packaging needs.
On the other hand, fully-automatic machines excel in high-volume operations, offering enhanced efficiency and consistency. By carefully considering your specific requirements, you can make an informed choice that optimizes your pallet wrapping process.
3. Evaluating Film Stretching Mechanisms: Pre-stretch vs. Power Pre-stretch
Film stretching mechanisms are critical components of pallet wrapping machines, as they determine the amount of film used to wrap each pallet load. In Australia, you will encounter two primary stretching methods: pre-stretch and power pre-stretch.
Understanding the differences between these mechanisms is vital to selecting the most suitable option for your packaging needs. Lets explore both pre-stretch and power pre-stretch mechanisms in detail, highlighting their advantages and potential drawbacks.
3.1 Pre-stretch Film Stretching Mechanism
Pre-stretch film stretching is a widely used method in pallet wrapping machines. This mechanism relies on mechanical means to elongate the stretch film before applying it to the pallet load. The film is stretched up to a certain percentage of its original length, reducing the overall amount of film required for each wrap.
Key points about pre-stretch film stretching include:
- Mechanical Rollers: Pre-stretch film mechanisms use mechanical rollers to stretch the film as it is dispensed from the roll. These rollers rotate at different speeds, creating the desired stretch.
- Stretch Percentage: The stretch percentage can be adjusted on the machine, typically ranging from 150% to 300% or more. Higher stretch percentages result in thinner film layers, reducing material costs.
- Film Yield: Pre-stretch mechanisms optimize film usage, resulting in higher film yield per roll and reducing the frequency of roll changes.
- Less Film Residue: Pre-stretch wrapping creates minimal film residue, contributing to a neater and cleaner wrap.
3.2 Power Pre-stretch Film Stretching Mechanism
Power pre-stretch film stretching takes the pre-stretch concept to a higher level by employing powered rollers to achieve higher stretch ratios and better control. This mechanism offers some distinct advantages over traditional pre-stretch methods:
- Motorized Rollers: Power pre-stretch systems use motorized rollers that can deliver higher levels of stretch, often exceeding 300% or even 400%. This allows for greater film economy and load stability.
- Consistency: Power pre-stretch mechanisms provide consistent stretching, ensuring uniform film distribution throughout the wrapping process.
- Enhanced Load Containment: The increased stretch capability of power pre-stretch mechanisms results in better load containment and reduced chances of load shifting during transportation.
- Thinner Film: With higher stretch ratios, power pre-stretch mechanisms produce thinner film layers, which not only save on material costs but also contribute to better load visibility and scanning capabilities.
3.3 Choosing Between Pre-stretch and Power Pre-stretch
Both pre-stretch and power pre-stretch film stretching mechanisms offer advantages in terms of film economy and load stability.
The decision between the two largely depends on your specific packaging requirements and budget considerations.
Consider the following points:
- Packaging Volume: For businesses with moderate packaging volumes, a pre-stretch mechanism may suffice. Power pre-stretch mechanisms are often more beneficial for high-volume operations.
- Load Characteristics: Evaluate the characteristics of the loads you typically handle. Power pre-stretch mechanisms may provide better load containment and stability for heavy or irregularly shaped loads.
- Budget Constraints: Pre-stretch mechanisms are generally more cost-effective than power pre-stretch systems. If budget is a significant concern, pre-stretch may be the preferred choice.
- Film Cost Savings: Calculate the potential film cost savings achieved through each mechanism based on your stretch percentage and wrapping volume.
The film stretching mechanism you choose can significantly impact your pallet wrapping process in terms of film economy and load stability. Pre-stretch mechanisms, with their mechanical rollers, are widely used and offer cost-effective film savings.
On the other hand, power pre-stretch systems provide even higher stretch ratios, enhanced load containment, and consistent film distribution.
By assessing your packaging volume, load characteristics, and budget constraints, you can select the most suitable film stretching mechanism for your pallet wrapping machine.
4. Capacity and Throughput Considerations for Pallet Wrapping Machines
Capacity and throughput are crucial factors to consider when choosing a pallet wrapping machine. Ensuring that the machine can handle your expected production levels without causing bottlenecks is essential for maintaining an efficient packaging process.
Lets delve into the concepts of capacity and throughput, as well as explore other related factors that impact the performance of your pallet wrapping machine.
4.1 Understanding Capacity and Throughput
- Capacity: Capacity refers to the maximum load weight and dimensions that the pallet wrapping machine can accommodate. It is essential to select a machine with a capacity that aligns with your typical load sizes to ensure smooth and efficient wrapping.
- Throughput: Throughput relates to the number of pallets the machine can wrap within a specific time frame. It is crucial to match the machine's throughput capability with your production requirements to prevent any potential bottlenecks in your packaging line.
4.2 Assessing Your Packaging Volume
To determine the appropriate capacity and throughput requirements, you must have a clear understanding of your packaging volume. Analyze the number of pallets wrapped per hour, day, or week. Consider any seasonal fluctuations or growth projections in your packaging volume. This information will help you select a machine that can handle your current and future demands efficiently.
4.3 Load Weight and Dimensions
The weight and dimensions of your typical pallet loads are vital factors that influence the machine's capacity.
Ensure that the machine's turntable size and weight capacity can accommodate the largest and heaviest loads you handle regularly. Additionally, consider the maximum height the machine can wrap to ensure compatibility with your tallest loads.
4.4 Wrapping Speed and Cycle Times
The wrapping speed of the machine directly impacts its throughput capabilities. Faster wrapping speeds are advantageous for high-volume operations, but be sure to balance speed with the quality of wrapping to maintain load stability. Additionally, consider the machine's cycle times—the time it takes to complete one wrapping cycle—when assessing its overall efficiency.
4.5 Multi-Shift Operations
If your packaging operation runs multiple shifts, take this into account when evaluating the machine's throughput. Machines with faster wrapping speeds and quicker cycle times can help meet the demands of multi-shift operations, ensuring continuous productivity.
4.6 Automation Features
Fully-automatic machines, with their automated load handling and wrapping processes, can significantly enhance throughput compared to semi-automatic machines. However, consider whether the level of automation aligns with your business needs and justifies the investment.
Choosing a pallet wrapping machine with the appropriate capacity and throughput is crucial for maintaining a smooth and efficient packaging process. By understanding your packaging volume, load characteristics, and operational requirements, you can select a machine that can handle your current and future demands. Additionally, consider the machine's wrapping speed and cycle times, as well as any automation features that may impact its overall performance.
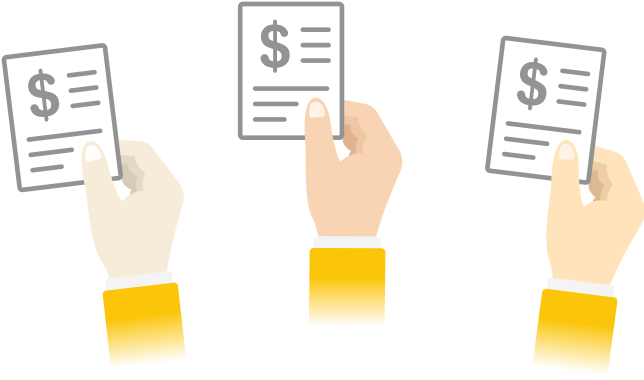
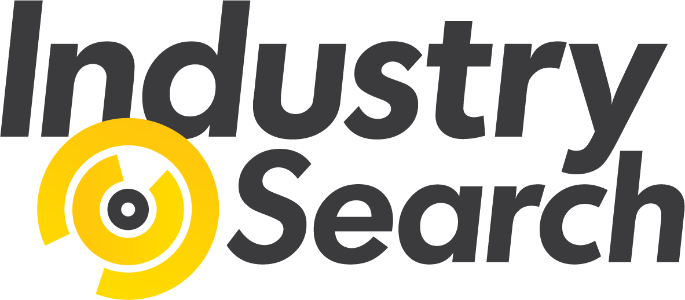
Find the right Pallet Wrapping Machine
Compare quotes from expert Australian suppliers and make the best choice. It's free, quick and easy!
5. Cost Analysis and Return on Investment (ROI) for Pallet Wrapping Machines
Investing in a pallet wrapping machine is a significant decision that requires careful cost analysis and consideration of the potential return on investment (ROI). While the initial investment may seem substantial, a well-chosen pallet wrapping machine can yield long-term cost savings and operational benefits. In this section, we will conduct a detailed cost analysis and explore the factors contributing to the ROI of pallet wrapping machines.
5.1 Initial Investment
The initial investment in a pallet wrapping machine includes the purchase cost, installation, and any required training for your staff. The price range of pallet wrapping machines can vary significantly depending on the type (semi-automatic or fully-automatic), features, and brand. While fully-automatic machines generally have a higher upfront cost than semi-automatic ones, they may offer greater benefits in terms of efficiency and labor savings.
5.2 Labor Savings
One of the most significant advantages of pallet wrapping machines is their potential to reduce labor costs. By automating the wrapping process, you can free up your employees for other tasks, potentially saving on labor expenses or reallocating labor resources to areas where they are more valuable.
5.3 Film Savings
The film stretching mechanisms, such as pre-stretch or power pre-stretch, contribute to film savings. Pre-stretch mechanisms mechanically elongate the film before wrapping, resulting in reduced film consumption per pallet. Power pre-stretch mechanisms take this further, achieving even higher stretch percentages and providing additional film economy.
5.4 Increased Efficiency and Productivity
Fully-automatic pallet wrapping machines can significantly increase your packaging line's efficiency and productivity. With higher wrapping speeds and reduced cycle times, these machines can handle a larger number of pallets per hour, ultimately enhancing your overall throughput.
5.5 Reduced Product Damage
Properly wrapped pallets offer better load stability and protection during transit, reducing the risk of product damage or loss. Investing in a high-quality pallet wrapping machine can contribute to lower product damage costs and improved customer satisfaction.
5.6 Maintenance and Operating Costs
Consider the maintenance and operating costs associated with the pallet wrapping machine. Regular maintenance ensures the machine's optimal performance and prolongs its lifespan. Additionally, assess the machine's energy consumption and film usage efficiency, as these factors can impact ongoing operating expenses.
5.7 Return on Investment (ROI)
Calculating the ROI for a pallet wrapping machine involves considering the initial investment, labor savings, film savings, increased efficiency, reduced product damage costs, and operating expenses over its expected lifespan. By comparing these potential benefits to the initial investment, you can determine the machine's payback period and long-term financial impact on your business.
A pallet wrapping machine's cost analysis and ROI assessment are essential steps in making an informed investment decision. Consider the initial investment, labor savings, film savings, increased efficiency, reduced product damage costs, and operating expenses to determine the machine's financial impact on your business.
Conclusion
Choosing the right pallet wrapping machine for your business in Australia requires a thoughtful and informed approach. Start by assessing your packaging needs and requirements, understanding your load characteristics, volume, and budget constraints. Then, explore the various features and film stretching mechanisms offered by different machines. Decide between semi-automatic and fully-automatic models based on your packaging volume, labor costs, and load variability. Consider the capacity, throughput, and automation features to ensure the machine can handle your operational demands effectively.
Furthermore, conduct a comprehensive cost analysis, taking into account the initial investment, labor and film savings, increased efficiency, reduced product damage costs, and ongoing operating expenses. By considering the potential return on investment, you can make a financially sound decision that optimizes your pallet wrapping process and contributes to your business's long-term success.
Purchasing a pallet wrapping machine is an investment in your packaging efficiency and overall productivity. By choosing the right machine that aligns with your unique business needs, you can streamline your packaging operations, enhance load stability, and reduce costs in the long run. Remember to stay informed about the latest advancements in pallet wrapping technology and keep an eye on your industry's best practices to ensure your business remains at the forefront of efficient packaging solutions.